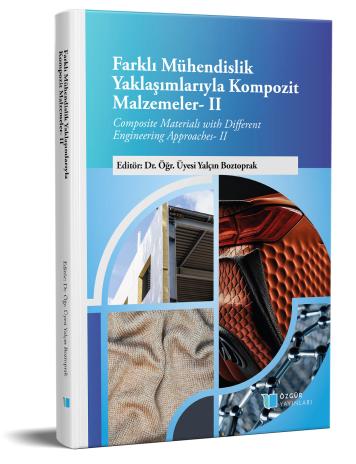
Alternatif Enerji Kaynakları Kullanılan Otoklav Yöntemi İçin Karşılaştırmalı Maliyet Analizleri
Şu kitabın bölümü:
Boztoprak,
Y.
(ed.)
2023.
Farklı Mühendislik Yaklaşımlarıyla Kompozit Malzemeler-II.
Özet
Çevresel etmenlerin en az enerji üretimi ve kullanımı kadar etkili olduğu günümüzde üretilen ürün başına tüketilen enerjinin yanında ürün başına çevreye verdiği emisyonlar da etkili olmaktadır. Bu nedenle üretim sektöründe yaygın olarak kullanılan tekniklerinin iyileştirilmesi bu sürece olumlu katkıda bulunacaktır. Bu çalışmada, kompozit üretiminde yaygın bir şekilde kullanılan otoklav fırınlar için alternatif enerjiler ve diğer enerjiler kullanılması ile karbon salımının minimize edilerek yatırım ve işletme maliyetleri gelecek piyasa koşulları için optimize edilmesi üzerine çalışılmıştır. Sistemde kullanılan enerji kaynağı olarak alternatif enerjiler ve doğal gaz kullanımı ile toplam enerji maliyetinin ve karbon salımının düşürüldüğü görülmüştür.